As a special storage form of natural gas, liquefied natural gas (LNG) has the characteristics of saving space and being conducive to long-distance transportation, which makes it occupy an increasing share in the supply of natural gas and develop rapidly. Liquefied natural gas is a low temperature liquid fuel, at standard atmospheric pressure, liquefied natural gas is -162 ℃. The volume is reduced to 1/625 of the original, which is equivalent to natural gas being compressed by 60MPa. The ignition point of LNG is 650°C, which is higher than that of gasoline and diesel, and its ignition energy is also higher than that of gasoline and diesel, so it is more difficult to ignite than gasoline and diesel; The explosion limit is 5% to 15%, and the density after vaporization is very low, only about half of that of air, so if there is a slight leakage, it will volatilize and spread immediately, and it is difficult to form a concentration that will burn and explode in case of fire.
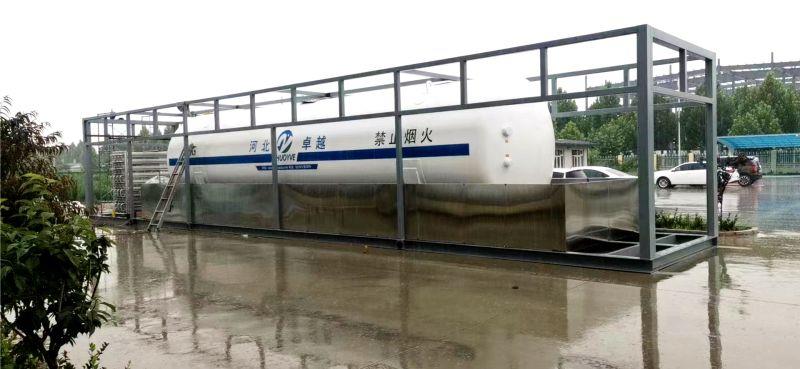
Natural gas liquefaction process
The natural gas liquefaction process can be divided into two categories according to the principle:
One is that the natural gas is compressed to increase the temperature of the gas, and then the heat is taken away by exchanging heat with the refrigerant. The refrigerant can be selected properly and the natural gas can be liquefied through several cooling stages;
The other type also raises the temperature of the gas through compression, removes the heat of the gas by heat exchange, and then depressurizes the gas through an expander or a throttle valve. According to the Joule-Thomson effect, the temperature of the gas is reduced, and the low-temperature gas exchanges heat with the gas before decompression, so that the decompressed gas can reach the liquefaction temperature.
Most of the natural gas liquefaction processes currently used in industry are a combination of the above two types of processes. Therefore, the liquefaction process of natural gas is essentially a process of continuously removing heat from natural gas through heat exchange.
Natural gas liquefaction process technology
At present, the liquefaction process technology of natural gas liquefaction devices in the world is mainly divided into three categories: expander refrigeration cycle technology, cascade refrigeration cycle technology and mixed refrigerant refrigeration cycle technology.
The first category is expander refrigeration cycle technology, which refers to the process of realizing natural gas liquefaction by using high-pressure refrigerant to expand adiabatically through a turboexpander Claude cycle refrigeration. While the gas expands and cools down in the expander, it can output work, which can be used to drive the compressor in the process. The key equipment in the process is the turbo expander. According to different refrigerants, it can be divided into nitrogen expansion liquefaction process, nitrogen-methane expansion liquefaction process, and natural gas expansion liquefaction process.
The advantage of the expander refrigeration cycle process is that the technology is mature and reliable. Compared with the multi-stage throttling mixed refrigerant refrigeration cycle process, it is simple, flexible to adjust, easy to start, easy to operate, and easy to maintain; there is no problem of refrigerant ratio (nitrogen expansion process and Methane expansion process), or simple ratio (nitrogen-methane expansion process), easy refrigerant replenishment. The disadvantage is that the unit energy consumption is the highest.
The liquefaction process with an expander is more suitable for natural gas liquefaction units with small capacity. The impact of operating energy consumption on the benefits of LNG plants is becoming more and more obvious. For the sake of energy saving, the liquefaction process with expander has been gradually eliminated in recent years.
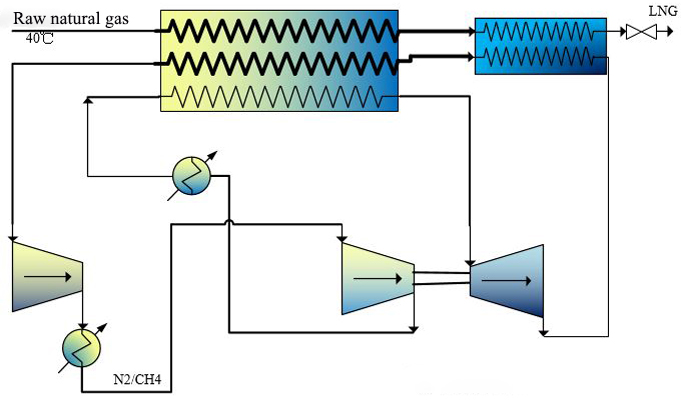
The second category is the cascade refrigeration cycle process, which is a more classic refrigeration cycle, also known as “step-by-step”, “cascaded” or “cascaded”. This cycle is composed of several different low-temperature The refrigeration cycle of the following operation is composed of cascades. Generally, it is formed by overlapping three refrigeration cycles of propane (or propylene), ethane (or ethylene) and methane to provide the cooling capacity required for liquefaction. Their refrigeration temperatures are -40°C, -100°C and -160°C, respectively. The advantage of the classic cascade refrigeration cycle is that it uses 3 kinds of refrigerants and 9 refrigeration temperature gradients (3 temperature levels for propane, ethane, and methane), so that the refrigeration temperature of each stage is close to the cooling curve of the raw material gas, reducing the Entropy, specific energy consumption is close to the upper limit of theoretical thermodynamic efficiency. Moreover, the process is flexible in operation, quick to start and stop, and easy to start and put into production at the initial stage. The pretreated natural gas enters the heat exchanger to exchange heat with C3H8, C2H4 and CH4 refrigerants respectively, after cooling, condensing, and throttling to normal pressure, it is sent to the liquefied natural gas storage tank for storage.
The advantages of the cascade refrigeration cycle are low energy consumption, the refrigerant is a pure substance, there is no matching problem, the technology is mature, and the operation is stable. The disadvantage is that there are many units and the process is complicated; there are many ancillary equipment, which are dedicated to storing refrigerant; the pipeline and control system are complicated and inconvenient to maintain.
The cascaded refrigeration cycle is suitable for large-scale natural gas liquefaction plants, and it is seldom used at present.
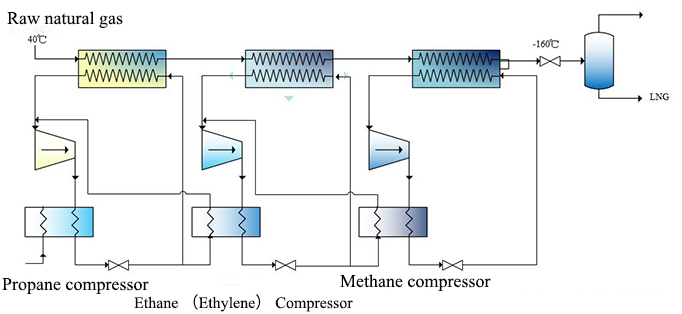
The third category is the mixed refrigerant refrigeration cycle process, which overcomes some shortcomings of the cascaded refrigeration cycle, and uses a mixed refrigerant and a refrigerant compressor. The refrigerant is prepared according to the natural gas components to be liquefied, and after being fully mixed, there are N2, C1-C5 hydrocarbons in it. Multi-component mixed refrigerant, step by step condensation, evaporation, throttling expansion to obtain cooling capacity at different temperature levels, so as to achieve the purpose of gradual cooling and liquefaction of natural gas.
The advantages of the mixed refrigerant refrigeration cycle are simple process, less equipment, low investment, and the investment is 15-20% less than the cascade refrigeration cycle; compared with the expander process, the unit energy consumption is 20%-30% lower; the disadvantage is that the energy consumption 10~20% higher than the cascade cycle.
The mixed refrigerant refrigeration cycle process has wide adaptability and can be suitable for large, medium and small natural gas liquefaction plants.
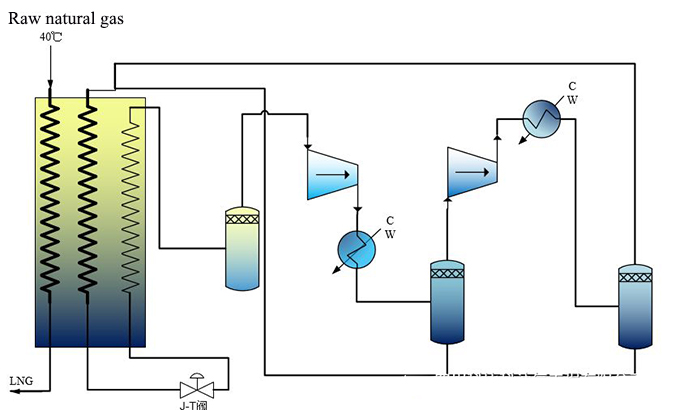
More details or any inquiries , click storage tank page