Overview
The surface of the finned tubes of the LNG air ambient vaporizer is greatly affected by the ambient air temperature and relative humidity. The gasification process absorbs the surrounding heat, resulting in a decrease in the ambient temperature and frosting. Lateral tension causes pipeline rupture, gas leakage, and accidents. At the same time, frost formation also affects the heat transfer performance of the gasifier. Therefore, it is very important to deeply study the frosting mechanism of LNG air-heated vaporizer, analyze its influencing factors and take effective control measures.
The LNG air-temperature vaporizer is composed of multiple finned tubes of the same type arranged side by side. Each finned tube is a star-shaped structure. The finned tube is composed of 8 fins or 12 fins (the finned tube in this paper is 12 Fins), the tubes are mostly low-temperature aluminum alloy, and the gasifier is mainly arranged vertically. The main structural parameters are shown in Table 1. The liquefied natural gas flows through the pipe from bottom to top. During the gasification process, it absorbs the heat of the surrounding environment and changes from a liquid state to a gaseous state. The temperature of the surrounding air outside the pipe drops. After a period of continuous operation, the vaporizer will frost. The thermal resistance of the frost layer Gradually increasing, seriously affecting the gasification efficiency of the gasifier. At present, the gasifier needs to be shut down and switched regularly, because the thermal resistance of the frost layer increases after frosting, and it needs to be shut down to defrost before it can continue to be used .
Finned tube inner diameter /mm | 18 |
Finned tube outer diameter /mm | 22 |
Finned tube length /mm | 8000 |
Fin thickness /mm | 2 |
Fin width /mm | 80 |
This paper only studies the frosting on the outer surface of the ambient vaporizer, and does not study the frosting between the finned tubes.
Vaporizer Frost Thickness Monitoring
Vaporizer monitoring point
In order to analyze the frosting around the vaporizer, the starting point is 50 cm from the ground at the fifth finned tube (middle) from the left end of the vaporizer, and 1.5 m, 3.0 m, and 4.5 m from bottom to top , 6.0 m position s to set four red spray paint monitoring points, which are respectively monitoring point 1 ,2, 3, 4, the layout of monitoring points is shown in Figure 1.
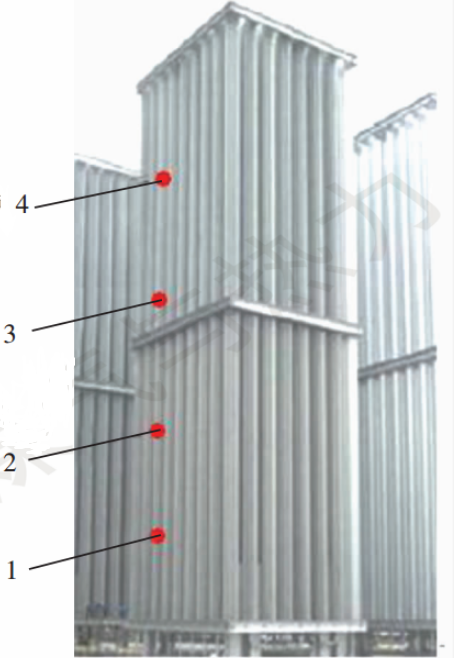
Vaporizer frost layer thickness measurement
During this test, the ambient air temperature around the vaporizer at the station was 8 °C, the relative air humidity was 76%, and the distance between the vaporizer was 3.5 m. For the frosted vaporizer, the vaporizer was operated continuously for 24 hours during the field test, and the thickness of the frost layer on the gasifier was measured. The measuring devices for the thickness of the frost layer mainly include an infrared range finder, cardboard and an elevator. The personnel use the infrared range finder and cardboard to carry the elevator to measure the thickness of the frost layer of the vaporizer regularly.
The specific method is as follows:
①Use the elevator to rise to each monitoring point respectively, and make corresponding marks;
②Put the cardboard against the position of the monitoring point, keep the cardboard parallel to the outer wall of the gasifier (the outer wall of the finned tube and round tube), and measure the distance from the outer wall of the gasifier to the cardboard by an infrared rangefinder , which is the thickness of the frost layer at the monitoring point;
③Measure and record the thickness of the frost layer at the four monitoring points respectively.
The relationship between the measured 24 h frost layer thickness and time in the vaporizer is shown in Fig. 2.
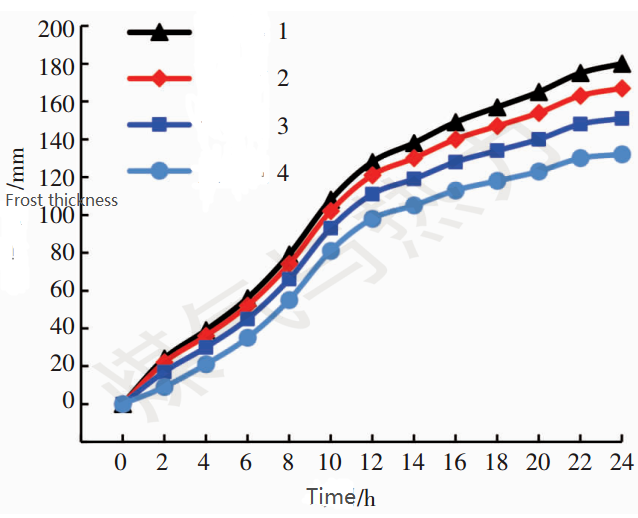
It can be seen from Figure 2 that the frosting of the vaporizer gradually extends from the bottom to the top of the gasifier, and the thickness of the frost layer gradually decreases. The maximum thickness of monitoring point 1 can reach 24 mm after the gasifier runs for 2 hours, and the thickness of the frost layer continues to increase as the gasifier continues to run. After 24 hours of operation, the maximum frost layer thickness at monitoring point 1 reached 180 mm. From monitoring point 1 to monitoring point 4, the maximum value of frost layer thickness decreases successively. From the field observation, the frosting length of the vaporizer reaches 7 950 mm, which is close to the total length of the gasifier (8 000 mm).
Mechanism of frosting in air ambient vaporizer
The frosting of the air-heated vaporizer is mainly caused by the water vapor in the air phase into solid crystals, and its geometric structure and accumulation law change with the frosting process, which makes the formation process of the frost layer very complicated, not a simple accumulation of crystals process. Through the analysis of the causes of frosting on the surface, the frosting process is divided into three stages: frost crystal growth period, frost layer growth period, and frost layer full growth period.
①Frost crystal growth period
During the frost crystal growth period, the water vapor in the air phase changes into a solid ice crystal structure. The frost crystal is a flat hexagonal structure.
②Frost growth period
The frost layer growth period refers to the gradual accumulation of solid ice crystals on the surface of the fins over time, developing into a dense frost crystal structure, and the thickness also increases rapidly. The rapid growth of the frost layer affects the gas circulation in the peripheral space of the vaporizer and hinders heat transfer. Therefore, the frost layer growth period is the best period to control the frost layer growth, and controlling the frost layer thickness during the frost layer growth period is very important.
③Full growth period of frost layer
As the vaporizer continues to operate, the temperature of the vaporizer decreases gradually, the frost layer accumulates thicker, and the hardness of the frost layer increases, and the frost layers of the fins are fully bonded together. At this time, the difficulty of manual defrosting increases.
Influencing Factors of Vaporizer Frosting
The frosting degree of the vaporizer is expressed by the thermal resistance of the frost layer. The main factors affecting the thermal resistance of the frost layer are air temperature, relative humidity of the air, and the distance between vaporizers, etc. All factors should be considered comprehensively in the design.
① Influence of air temperature
During the test, the relative humidity of the air was kept at 76%, and the distance between the gasifiers was kept at 3.5 m. The air temperature around the gasifier to be tested can be reduced by running the other 3 gasifiers, and monitored in real time with a thermometer. When the specified air temperature is reached, start a gasifier to be tested without frost. When the time is 0, start counting. At the same time, the air temperature around the gasifier to be tested was controlled by adjusting the operating conditions of the other three gasifiers, so that it was maintained at the specified measurement air temperature during the 24-hour operation. When running to the 24th hour, measure the frost layer thickness at each monitoring point. Change the specified measurement air temperature, repeat the above operation steps, and measure the thickness of the frost layer at the 24th hour under different air temperatures. In the case that the ambient air temperature around the gasifier is a single variable, the frost layer thermal resistance at different temperatures is calculated by formulas, as shown in Figure 3.
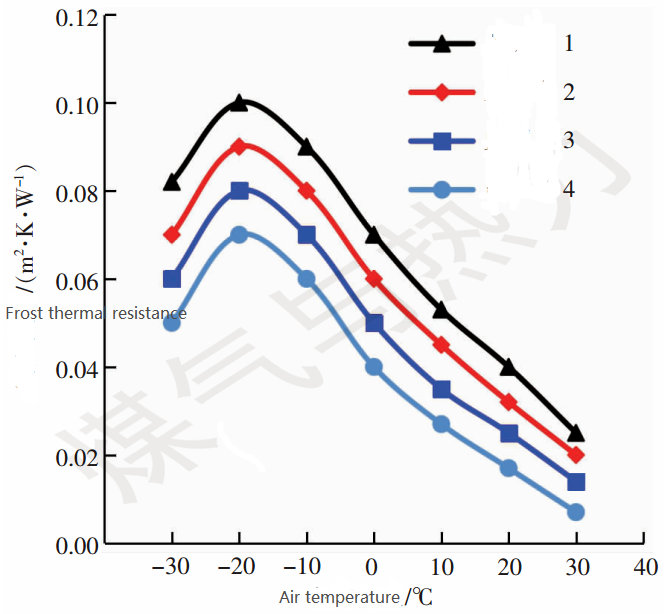
It can be seen that as the air temperature decreases, the thermal resistance of the frost layer increases first and then decreases. The greater the thermal resistance of the frost layer, the lower the heat transfer performance of the vaporizer and the lower the gasification efficiency.
②Influence of air relative humidity
During the test, the air temperature was kept at 8 °C and the distance between gasifiers was kept at 3.5 m. Different air relative humidity can be achieved by humidifier or water sprayer. When the relative humidity of the ambient air around the vaporizer reaches the specified relative humidity of the measured air, start a non-frosting vaporizer to be tested. At this time, it is 0 time and start timing. At the same time, the relative humidity of the air has been maintained at the specified relative humidity of the measured air during the 24-hour operation. When running to the 24th hour, measure the frost layer thickness at each monitoring point. Change the specified measured air relative humidity, repeat the above steps, and measure the thickness of the frost layer at the 24th hour under different air relative humidity. When the relative air humidity is a single variable, the thermal resistance of the frost layer at the 24th hour under different relative air humidity is obtained, as shown in Figure 4. It can be seen that as the relative air humidity increases, the thermal resistance of the frost layer first increases and then decreases. When the relative air humidity reaches about 30%, it has a great influence on the heat transfer performance of the vaporizer.
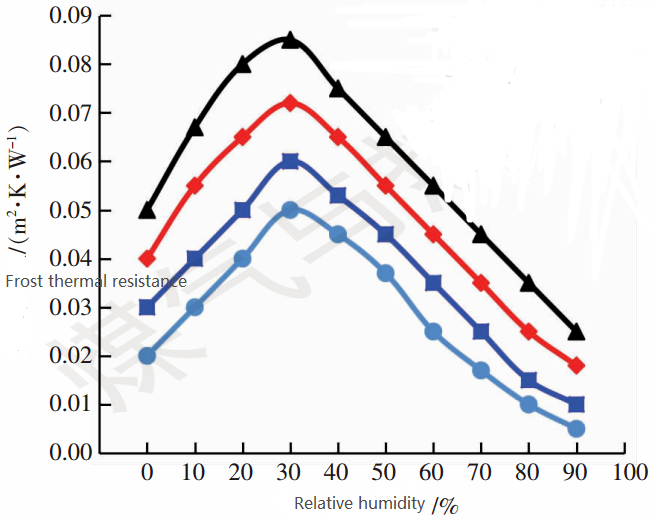
③ Influence of vaporizer spacing
The distance between the gasifiers (the distance from the outer wall to the outer wall) also has a certain influence on the frosting. The main consideration is the influence of the air circulation around multiple gasifiers on the frosting. In Chongqing area, gasification stations with different gasifier spacings were selected for field research, and the thickness of frost layer was measured. During the test, keep the air temperature at 8 °C and the relative air humidity at 76%. Start a non-frosting gasifier to be tested, at this time, it is 0 time, and start timing. When running to the 24th hour, measure the frost layer thickness at each monitoring point. For gasification stations with different gasifier spacings, repeat the above steps, and measure the thickness of the frost layer at the 24th hour under different gasifier spacings. When the gasifier spacing is a single variable, the thermal resistance of the frost layer at the 24th hour under different gasifier spacing is calculated, as shown in Fig. 5.
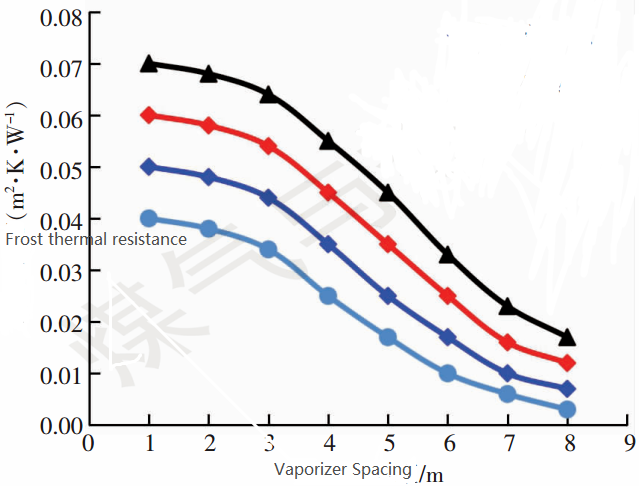
It can be seen that with the increase of the distance between the gasifiers, the thermal resistance of the frost layer decreases gradually. Through the actual investigation of several gasification stations, considering factors such as the occupied area, the distance between gasifiers should be 3-5 m.
④Summary
To sum up, the three influencing factors are sorted from large to small according to their corresponding maximum value of frost layer thermal resistance, the order is air temperature, air relative humidity, vaporizer distance, and the corresponding maximum value of frost layer thermal resistance is 0.100, 0.085, 0.070 m2 K/W. Therefore, the air temperature has the greatest influence on the thermal resistance of the frost layer.
Control Technology and Application
①Air temperature control
According to the analysis of the above influencing factors, the prevention of frosting in the vaporizer can be solved by increasing the air temperature. The purpose of increasing the air temperature is to suppress the formation of frost in the vaporizer. Therefore, steam heating can be used to spray hot steam around the gasifier to increase the air temperature, thereby inhibiting the formation of frost.
② Air relative humidity control
When the gasifier is running, it will absorb the surrounding heat and produce a large amount of white mist, which will increase the relative humidity of the surrounding air. If it is not treated in time, it will further condense into frost around the gasifier. Mechanical mist removal can be adopted to increase air circulation, and four explosion-proof fans with a power of 2.2 kW are arranged at a position 3-5 m away from the vaporizer on the ground at the liquid inlet end of the vaporizer for mechanical mist removal to increase air circulation , to blow away the generated white mist, thereby reducing the relative humidity of the air. According to on-site measurements, the relative air humidity can be reduced to about 8% by using 4 sets of the above-mentioned explosion-proof fans, which effectively reduces the influence of relative air humidity on the frosting of the vaporizer. The actual layout of the explosion-proof fan site is shown in Figure 6.
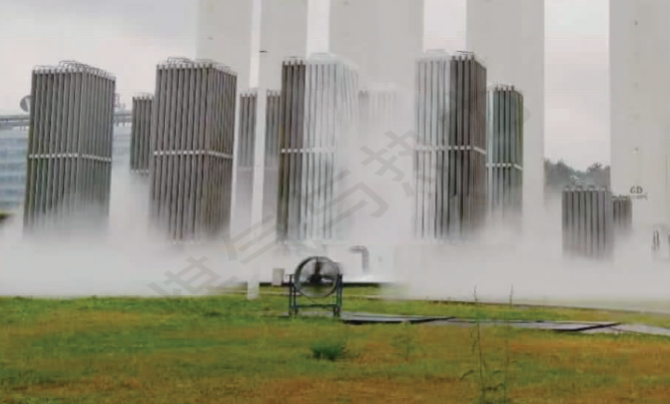
③Vaporizer spacing control
At present, most of the gasification stations have small sites, some gasifiers are close to each other, the air circulation is poor, and the water vapor in the air is difficult to diffuse. Therefore, frost is easy to form when the temperature is too low. When the gasifier is arranged, the distance between the gasifiers should be at least 3 m to ensure sufficient air circulation and reduce the rate of frosting.
④SCADA intelligent monitoring system control
In the gasification area of the gasification station, the SCADA intelligent monitoring system can be used to monitor the temperature, pressure, gasification volume and other parameters of the gasifier inlet and outlet in real time. When the temperature in the gasifier tube is low and the gasifier is frosted, the gasifier group can be switched in time to reduce the rate of frosting of the gasifier, and at the same time ensure the continuous operation of the gasifier without affecting the normal gas supply.
Conclusion
① Analyze the frosting mechanism of the LNG air-temperature vaporizer, and divide the frosting process into frost crystal growth period, frost layer growth period, and frost layer full growth period. The frost layer growth period should be strictly controlled to prevent large area of the gasifier frost.
② Sampling was taken at the LNG gasification station, and the porosity of the frost layer was found to be 6.13% through actual measurement.
③ Analyze the influence of air temperature, air relative humidity, and gasifier spacing on gasifier frosting. Through actual measurement of the thickness of the frost layer, the variation law of the thermal resistance of the gasifier frost layer with the influencing factors is calculated, and the effect of air temperature on gasification The frost layer thermal resistance of the vaporizer has the greatest influence, so the air temperature around the vaporizer must be strictly controlled.
④ Put forward the control measures to reduce the frosting of the gasifier (steam heating the air around the gasifier, mechanical mist removal, control of the distance between gasifiers, and SCADA intelligent monitoring). The operation practice shows that after the control measures are taken, the gasifier is effectively controlled The frosting phenomenon, the thickness of the frost layer and the length of the frosting are obviously reduced.