100% radiographic flaw detection (RT) is carried out on the weld seam inspection of the container in the storage tank, and then the penetration test, air pressure test and air tightness test are carried out, and finally the helium mass spectrometry is carried out on each weld seam and joint by the “helium mass spectrometer leak detector”. leak detection.
The container in the storage tank is cleaned as a whole, and the cleanliness is treated according to the oxygen standard, and it is tested by ultraviolet light to ensure that there is no oil stain and other organic impurities.
The time interval between the cleaning and drying of the inner container of the storage tank and the pairing with the outer container is less than 3 hours to prevent dust and other organic impurities from entering and ensure the cleanliness of the inner container and the jacket.
The outer container of the storage tank shall be inspected by 20% radiographic flaw detection (RT) for the weld seam first, and then the interlayer shall be tested for air tightness and helium leak detection.
The inner and outer surfaces of the outer container of the storage tank are sandblasted to meet the requirements of the Sa-2.5a standard. After the surface of the steel plate is metallic, the dust attached to the surface is completely sucked off by a vacuum cleaner, so as to ensure the stability of the vacuum degree in the interlayer; The finished paint film on the outer surface of the tank is dense, firm and reliable, and the dry film thickness of the paint is greater than 200µm, ensuring that it will not fade within at least 3 years.
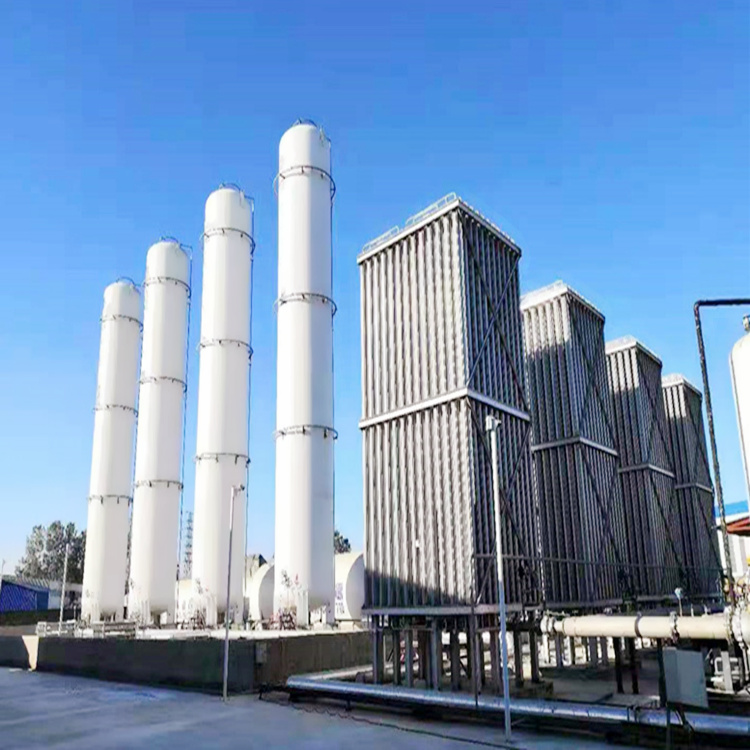
Wanna more details or send inquiry ? Just click bottom button